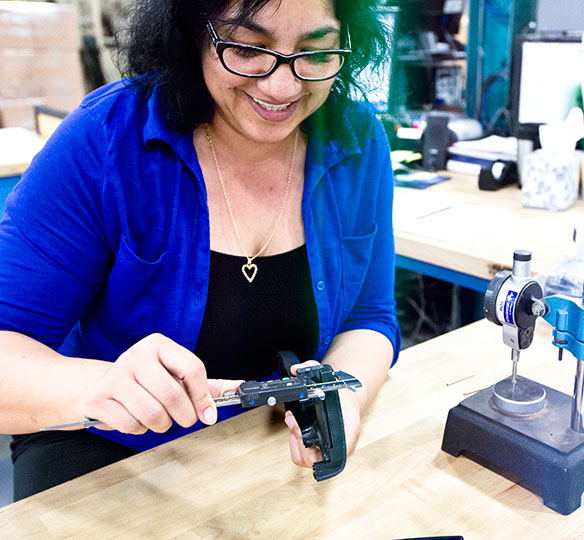
All of our manufacturing facilities are ISO 13485 compliant. We utilize a variety of quality tools and control systems to ensure we meet our customers’ quality needs and finished product specifications. From incoming raw material inspection, to finished product release and validation testing, our quality personnel and ERP system control all aspects of the production process.
Our process of quality assurance starts with the design of the product and production system. Our engineers collaborate with our customers and make recommendations on materials, tools, and design modifications to improve product manufacturability. Our suppliers and partners are all carefully qualified and managed to ensure raw materials meet the standards required to produce the highest quality output. We also utilize CAPA, complaint handling, and process controls to ensure that we are producing the highest quality, conforming parts.
At Biomerics we understand that a carefully constructed process should be methodically validated, audited, and improved–which is why we utilize advanced technologies and methodologies throughout each production run to ensure the highest quality product. We utilize the following processes and tools to enhance and ensure quality performance:
Problem Solving & Operational Quality:
- Six Sigma Problem Solving Tools (DMAIC, 8D)
- Work Flow Diagrams/Process Mapping
- 5 Why’s
- Ishikawa Diagrams
- Cause and Effect Matrix
- Is/Is Not Analysis
- Pareto Analysis
- Control Plans/Charts
- Standard Work Documentation
Development & Validation
- Design Development Planning
- Risk Analysis and Risk Assessment (aFMEA / dFMEA / pFMEA)
- First Article Layouts and Approvals
- Process Capability Studies (CpK, PpK, Tolerance Intervals)
- IQ, OQ, PQ Validations
- Lab testing for Analysis and Compliance